
Serial Vs Parallel Dilution Method In Bod
Private well waters were analyzed by a five-tube, three-dilution MPN method employing LB. Waste and surface waters were analyzed by a five-tube, five-dilution MPN method employing LB. Ten microliters from tubes of LB exhibiting acid and gas production was loop inoculated to LTLSB and to brilliant green LB (BG). Jan 20, 2014 - The prediction capability of C1 for TOC, BOD, and COD were improved. Combined with parallel factor analysis, an advanced data treatment technique. Sulfate equivalents (QSE) using the fluorescence of a diluted series of. Zig ziglar carti pdf in romana.
Primary mechanism for heat loss during exercise ( roughly 80%) An increase in core body temperature causes an increase in sweat production from sweat glands. Heat is transferred to the environment as sweat on the skin is converted from a liquid to a vapor. Mos def discography. ONLY lose heat from sweat that is vaporized not from sweat that drips off the body. Skin that is cooled off from evaporation transfers the loss of heat to blood flowing through the layer underneath the skin and ultimately to the core.
Sweat that is evaporated straight into the air from the skin produces the most heat loss. ( clothes may produce heat loss but not as much). In the cold substrate utilization shifts to a greater reliance on carbs Lower VO2 Max and higher metabolism represents a higher percentage of max capacity.Since carbs are preferred at higher intensities it leads to greater utilization of glycogen Prolonged endurance events the greater reliance on carbs will most likely lead to early onset fatigue Also, blood flow to the periphery is reduced which lowers oxygen levels in the muscle and the oxidative pathway. So higher levels of blood lactate are often seen during cold environment exercising.
March 15, 2007 Many laboratory protocols require the serial dilution of reagents or compounds. IC50 assays, commonly used to evaluate drug efficacy, and assay development procedures, as well as standard-curve generation, involve the serial dilution of compounds, proteins, or detection agents. These processes can be streamlined by utilizing automated liquid-handling equipment with serial dilution capabilities. Serial dilution processes face two major challenges.
The first is error propagation across columns or rows. With each sequential serial dilution step, transfer inaccuracies lead to less accurate and less precise dispensing. The result is that the highest dilutions will have the most inaccurate results. To compensate for this error possibility, longer mixing times are required, which then increases the time required to perform the serial dilution.
These challenges greatly limit the throughput capacity of an automated serial dilution system. To overcome these challenges, the effects of various mixing parameters of a serial dilution protocol were explored. Velocity11’s (www.velocity11.com) Bravo™ Liquid Handling Platform performed serial dilution with the same pipette head as a full plate dispenser (Figure 1).
With the platform’s VWorks™ software, the application allowed the total control of liquid transfer and mixing heights and speeds, which allowed efficient exploration of mixing parameters. The goals were to determine which parameters had the greatest effect on mixing and to reduce the time required to perform a serial dilution. Serial Dilution Mix Cycles. The basic experiment diluted fluorescein across the columns of a 96-well plate, from A1 to A10 (A11 and A12 were blank wells). The starting volume was 300 µL, and 200 µL tips were utilized for the transfer (150 µL, a 1:2 dilution) and mixing steps (190 µL).
There are two main components of an accurate and precise serial dilution: the accuracy and precision of the transfer and the efficiency of mixing. Transfers were previously determined to have a precision and accuracy of >99% at this volume; any observed deviations in precision and accuracy were due to error propagation from ineffective mixing. Two measures were used to evaluate mixing efficiency.
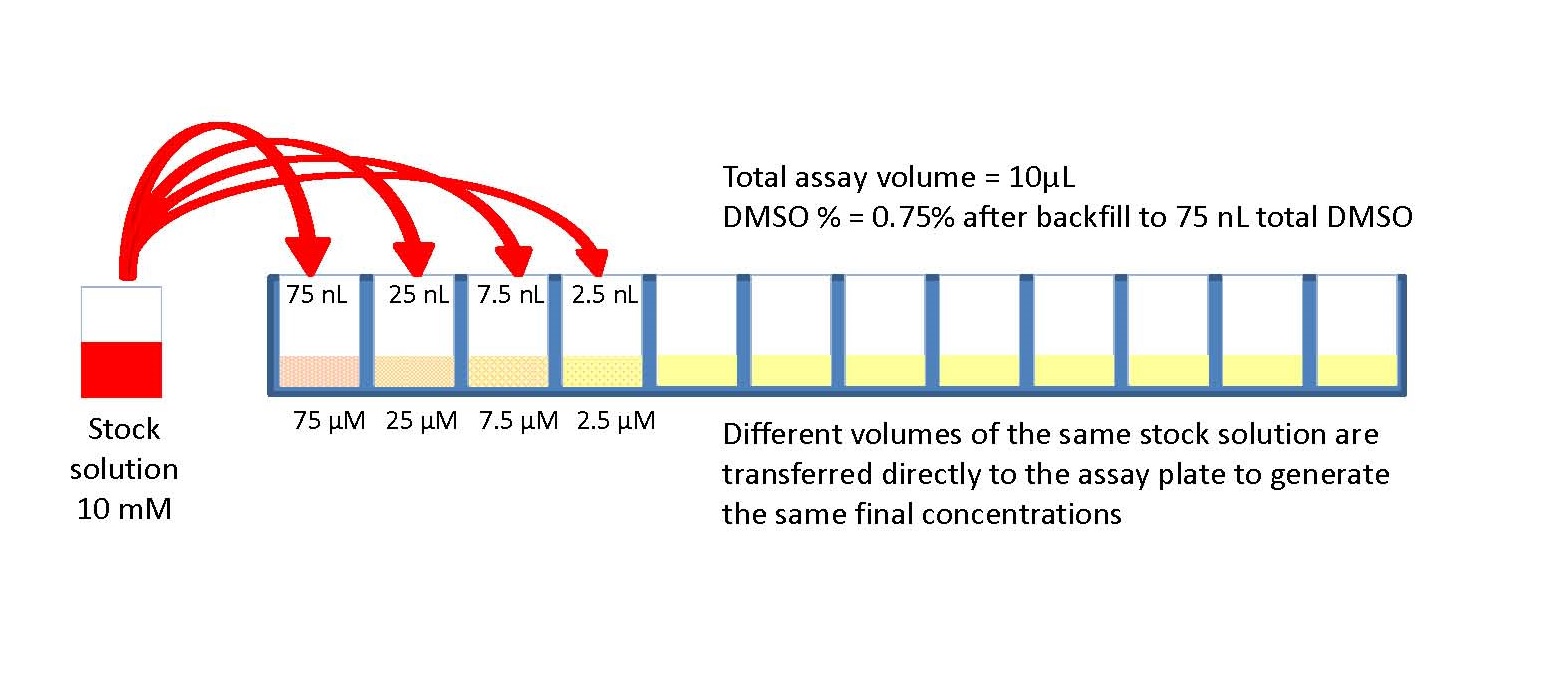
The Coefficient of Variance (CV) of each column indicated the precision of the mixing step. The CV also provided information on the propagation of error across a plate—the CV increased sharply across the plate if mixing was incomplete. The second indication was the accuracy of the transfer. A calibration curve was prepared, and each experimental dilution concentration was plotted against the standard curve to determine the real concentrations in each column.
The first experiment varied the number of mixing cycles between 3 and 20. The average precision (averaging CVs for columns 1–10) improved asymptotically as the number of mix cycles increased. Three mixes before each transfer yielded an average CV of 11.8%, while 20 mixes gave a considerably better CV of 1.7%. The precision in all cases generally worsened as the serial dilution proceeded across the plate; this was expected as the error in the earlier columns propagated with each transfer.